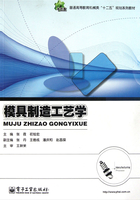
1.4 模具的分类与主要加工方法
在工业生产中,为适应不同制品零件的用途及生产,模具的种类很多。根据成型方法、材料和设备的不同,模具可分为冲压模具和型腔模具两大类。型腔模具又可分为塑料模、锻模、压铸模、粉末冶金模、陶瓷模、橡胶模、玻璃模等。模具的主要分类见表1-1。
表1-1 模具的分类
1.冲压模具
冲压模具简称冲模,它是对金属板料或型材进行冲压加工的模具,也可以冲压一些非金属板料。其使用的配套成型设备是压力机。
在冷冲压生产中,冲模又分很多种。按工序性质不同,可分为冲裁模、弯曲模、拉深模、成型模、冷挤压模等;按工序组合方式,可分为单工序冲模、连续模和复合模等;按冲模导向方式,可分为无导向冲模、有导向冲模;按模具使用材料,可分为钢制冲模、钢板模、硬质合金冲模及低熔点合金冲模、锌基合金冲模、橡胶冲模等;按生产适应性,可分为通用冲模、组合冲模、专用冲模等;按机械化程度,可分为手工操作冲模、半自动冲模及自动冲模等;按生产管理形式,可分为小型冲模、中型及大型冲模等。
下面以冷冲模为例,说明其成型过程及特点。冷冲模是指在室温下把金属或非金属板料放在模具内,通过压力机和模具对板料施加压力,使板料发生分离或变形制成所需零件的模具。下面介绍各类冷冲模成型的特点。
(1)冲裁模
冲裁模可将一部分材料与另一部分材料分离。图1-1所示为落料模结构形式,它的成型特点是将材料封闭的轮廓分开,而最终得到的是一平整的零件。图1-2所示为一冲孔模结构,它是将零件内的材料与封闭的轮廓分离,使零件得到孔。
(2)弯曲模
弯曲模可将板料或冲裁后的坯料通过压力在模具内弯成一定的角度和形状。图1-3所示的弯曲模是将平直的板料压成带有一定角度的弯曲形状。
(3)拉深模
拉深模可将经过冲裁所得到的平板坯料,压制成开口的空心零件。图1-4所示的模具是将平板的坯料拉深成筒形零件。

图1-1 落料模
1-凸模;2-凹模;3-模座;4-板料

图1-2 冲孔模
l-模柄;2-凸模;3-凹模;4-模座;5-定位板

图1-3 弯曲模
l-凸模;2-凹模

图1-4 拉深模
l-凸模;2-凹模
(4)成型模
成型模是用各种局部变形的方法来改变零件或坯料的形状。图1-5所示的是将空心件或管件毛坯的端部由外向内压缩,以缩小其口径成为所要求的零件形状。
(5)冷挤压模
冷挤压模是室温下在模具型腔内将金属坯料加压,使其产生塑性变形,挤压成所需的形状、尺寸及性能的零件。图1-6所示的是将一部分金属在压力作用下,冲挤到凸凹模形成的型腔内,使毛坯变成所需要的空心零件。

图1-5 成型模
1-凸模;2-凹模;3-顶件器

图1-6 冷挤压模
l-凹模;2-凸模
2.型腔模具
型腔模是指将金属或非金属材料经加热或熔融后,填入模具型腔内,经一定压力并冷却后而形成与型腔相应形状的零件的一种模具。
(1)塑料模
塑料模是将塑料原料制成塑料制件的模具。在工业生产中,塑料可分为热固性塑料和热塑性塑料两大类。热固性塑料加热即能固化,但一旦固化即使再加热也不再软化;热塑性塑料则加热即软化,冷却即固化。因此,塑料模又分为热固性塑料压缩模、压注模和热塑性塑料注射模及挤塑模、吹塑模、吸塑模、发泡成型模等多种结构形式。无论采用哪种形式模具成型零件,从原理上都要使塑料经过熔化、流动、固化三个阶段。
常见塑料模的成型过程如下:
① 压缩模的成型过程。将热固性塑料放在模具型腔内,在压力机上通过加热板对其加热、加压后使其软化充满型腔,经保温、保压一定时间后,软化的塑料就固化成与型腔相应形状的零件,如图1-7所示。
② 挤塑模的成型过程。将塑料放入专用的加料室内,通过压力机加热、加压,使受热而软化的塑料经过浇注系统挤入模具型腔内,待型腔填满固化后即可形成所需的零件,如图1-8所示。

图1-7 塑料压缩模
1-上模;2-下模;3-模套

图1-8 塑料挤塑模
1-压料柱塞;2-浇注口模板;3-加料室;4-型腔
③ 注射模的成型过程 将热塑性塑料放入专用的注射机料筒内,通过加热使其熔化成流动状态,再以较高的速度和压力,通过推杆将其注入模具型腔内,待其固化后,形成所需要的零件,如图1-9所示。
(2)锻模
锻模是在锻压设备上实现模锻工艺的装备,是热模锻的主要工具。根据使用设备的不同,锻模又可分为锤锻模、机械压力机锻模、螺旋压力机锻模、平锻模、胎模等多种类型。锻模的成型过程如图l-10所示,将金属毛坯加热后放在模膛内,利用锻锤的压力使材料发生塑性变形,待充满型腔后,形成所要求形状的零件。

图1-9 塑料注射模
1-注射筒;2-模具型腔

图1-10 锻模
1、2-锻模模膛
(3)压铸模
压铸模是用压力铸造方法获得锡、铅、锌、铝、镁、铜等各种合金材料铸件的模具。如图1-11所示,把经加热熔化成液体的有色金属合金,放入压铸机的加料室内,用压铸机活塞加压后使其进入模具型腔内,待冷却后固化成所需要的形状的零件。采用压铸模成型的铸件表面光洁、轮廓清晰,尺寸及形状稳定、精度较高。
(4)粉末冶金模
粉末冶金模是将金属粉末压制成制品零件的模具。根据成型零件的材料、性能、形状及精度要求,粉末冶金模又分为常温压模、加热压模及无压成型模、注射成型模等多种类型。而每种类型,根据其成型特点又分为成型、整型、挤压、热压、热挤、散装烧结、冷冻成型等多种结构形式。粉末冶金模的成型过程如图1-12所示,将混料后的合金粉末或金属粉末放入模内进行高压成型成坯件,然后将坯件在熔融点以下的温度加热烧结而形成金属零件。

图1-11 合金压铸模
1-加料室;2-模具型腔图

图1-12 粉末冶金模
1-底座;2-料斗;3-压块;4-模套;5-型腔凹模
(5)橡胶模
橡胶模是将天然橡胶或合成橡胶制成橡胶成型件的模具。根据其成型方法不同,橡胶模又分为压制模、压注模、注射模三种结构类型。但无论采用哪种类型,都应先将橡胶加热硫化后,设法灌入模具型腔内,经加压、保压而成型。橡胶模的成型过程如图1-13所示,将预先压延好的胶料按一定形状、尺寸下料后,直接装入模具型腔内,合模后在平板硫化机或液压机上按规定的压力和温度进行压制,使胶料在受热、受压下呈现塑性流动充满型腔,保持一定时间后而经硫化制成所需要的零件。
(6)玻璃模
玻璃模是使熔融的玻璃原料成型所使用的模具。如制造瓶类零件的玻璃模,一般为瓶口直径比胴体直径小,所以,为了便于脱出制件,模具往往制成铰接对合结构。玻璃模的成型过程如图1-14所示,将熔融的玻璃原材料放入模具型腔内,利用压制或压缩空气压制或吹压使其贴近模具型腔,经冷却后而形成零件。
3.模具的加工方法
制造模具的材料主要是金属材料。制造模具的方法很多,将金属材料加工成模具的方法主要有机械加工、特种加工、塑性加工和铸造等。作为工艺装备的模具,它不同于一般机械产品的制造,由于模具多为单件生产,同时模具还具有使用精度和制造要求高的特点。因此,模具的加工主要采用机械加工和特种加工。
(1)机械加工
机械加工即传统的切削与磨削加工,是模具制造中不可缺少的一种重要加工方法,即使采用其他方法加工制造模具,机械加工也常作为零件粗加工和半精加工的主要方法。

图1-13 橡胶模
1-上模;2-型芯;3-凹模套

图1-14 玻璃模
1-下模型芯;2-型腔;3-上模型芯;4-模套
机械加工主要采用普通机床、仿形铣床、仿形刨床、成型磨床及数控机床等进行加工。其主要特点是加工精度和生产率高,通用性好,用相同的设备和工具可以加工出各种形状和尺寸的工件。但加工形状复杂的工件时,加工速度很慢,且高硬度材料难以加工。
根据模具零件所达到的加工精度,切削加工工艺又分为粗加工工序、精加工工序及整修加工工序。
粗加工工序是指在加工中从工件上切去大部分加工余量,使其形状和尺寸接近成品要求的工序。如粗车、粗镗、粗铣、粗刨及钻孔等,其加工精度低于IT11,表面粗糙度大于Ra6.3μm。粗加工工序主要用于要求不高,或非表面配合的最终加工以及作为精加工之前的预加工。
精加工工序是从经过粗加工的表面上切去较少的加工余量,使工件达到较高的加工精度及表面质量。常用的加工方法主要有精车、精镗、铰孔、磨孔、电加工及成型磨削等。
整修加工是从经过精加工的工件表面上除去很少的加工余量,以得到较高精度及表面质量的零件,此工序一般为零件加工的最终工序,其精度及表面质量要求应达到模具设计图样的要求,如导柱、导套的研磨,工作成型零件的抛光等。
(2)特种加工
特种加工是直接利用电能、声能、光能、化学能等来去除工件上的余量,以达到一定形状、尺寸和表面粗糙度要求的加工方法。它主要包括电火花成型加工、电火花线切割加工、电化学加工、超声波加工、激光加工等。
特种加工与传统机械加工方法不同,它具有如下特点:
① 加工情况与工件的硬度无关,可以实现以柔克刚;
② 工具与工件一般不接触,加工过程不必施加明显的机械力;
③ 可加工各种复杂形状的零件;
④ 易于实现加工过程自动化。
基于以上优点,特种加工在模具制造中得到越来越广泛的应用,并成为模具加工中的一种重要方法。
(3)塑性加工
塑性加工主要是指模具型腔的挤压成型,有冷挤压、热挤压和超塑挤压成型等方法。随着模具制造工艺的发展和新型模具材料的出现,目前,除了传统的切削加工方法和特种加工方法之外,挤压成型制模技术在模具制造领域也得到了越来越广泛的应用。
1)冷挤压成型
冷挤压成型是在常温下利用安装在压力机上的冲头,以一定的压力和速度挤压模坯金属,使其产生塑性变形而形成具有一定几何形状和尺寸的模具型腔。该方法具有制造周期短、生产率高、型腔精度高、模具寿命长等优点,但变形抗力大,需要大吨位的压力机。型腔冷挤压成型技术广泛应用于小尺寸浅型腔模具及难以机械加工的复杂型腔模具的制造,同时还可以用于有文字、花纹、多型腔模具的加工,详细工艺见第6章的6.4.4节。
2)热挤压成型
热挤压成型是将模坯加热到锻造温度后,用预先准备好的模芯压入模坯而挤压出型腔的方法。热挤压成型模具,制造方法简单、周期短、成本低,所形成的型腔内部纤维连续、组织细密,因而耐磨性好、强度高、使用寿命长。但由于模坯加热温度高,尺寸难以掌握,易出现氧化等缺陷,所以,热挤压成型技术常用于尺寸精度要求不高的锻模制造。
模芯可以用工件本身或事先专门加工制造。用工件作为模芯时,由于未考虑冷缩量,因此,只适用于几何形状、尺寸精度要求不高的锻件的生产,如起重吊钩、吊环螺钉等产品。当工件形状复杂且尺寸精度要求较高时,必须设计、制造模芯。模芯的所有尺寸应按锻件尺寸放出锻件本身及型腔的收缩量,一般取1.5%~2.0%,并做出起模斜度。因为考虑到分模面的后续加工,在高度方向上应加上5~15mm的加工余量。模芯材料一般为T7、T8或5CrMnMo等,热处理硬度达到50~55HRC。图1-15所示为热挤压成型起重吊钩锻模示意图。用吊钩本身作模芯,先用砂轮打磨表面并涂上润滑剂后,放在加热好的上、下模坯之间,施加压力挤压出型腔。
3)超塑挤压成型
超塑挤压成型是利用材料在超塑性态下,以成型冲头将型腔挤压成型的方法。某些金属材料在特定的条件下具有特别好的塑性,凡伸长率δ超过100%的材料均称为超塑性材料。到目前为止,共发现一百多种超塑性金属,其中以有色金属为主,常用于模具制造的超塑性金属为ZnAl22。这种材料在360℃以上时快速冷却,可获得5μm以下的超细晶粒组织,当变形温度处在250℃时,伸长率可达300%以上,即进入超塑性状态。
发生超塑变形的速度和温度有一定的范围。一般来说,当温度超过材料熔点的1/2时,在一定的温度范围内即具有超塑性;超塑性变形的最佳速度为0.1mm/min以下。经超塑成型后,要进行强化处理,使材料超塑性消失,并获得较高的力学性能。
图1-16所示为超塑性挤压模具示意图,用成型的冲头压入超塑性材料,合金的流动性和填充性得到充分发挥,便可复制出与冲头形状相一致的凹型腔。加热炉配有自动控温仪表,以保证加压过程中坯料和冲头等保持恒温。
超塑成型的模具型腔或型芯,基本没有残余应力,尺寸精度高、稳定性高、材料的变形抗力小,与冷挤压相比,可极大地降低工作压力。利用超塑成型技术制造模具从设计到加工都得到简化,材料消耗减少,可使模具成本降低。
(4)铸造加工
铸造是将液态金属浇注到具有与零件形状、尺寸相适应的铸型型腔中,待其冷却后凝固,以获得毛坯或零件的生产方法。铸造可制成形状复杂、特别是具有复杂内腔的模具零件的毛坯。铸件加工余量小,节约金属,减少切削加工量,从而降低制造成本。
模具零件的铸造工艺可分为四种类型,即砂型铸造、陶瓷铸造、压力铸造及实型铸造。具体使用哪一种取决于模具的尺寸、加工精度以及要达到的表面粗糙度。

图1-15 热挤压成型吊钩锻模
1-上砧;2-上模坯;3-模芯;4-下模坯;5-下砧

图1-16 超塑挤压模具示意图
1、3、6-隔热板;2、7-水冷板;4-热电偶;5-加热炉;8-顶杆;9-下垫板;10-防护套;11-顶板;12-模坯;13-凸模;14-固定板;15-上垫板
砂型铸造是传统的铸造方法工艺,主要用于精度和使用寿命要求不高的大型模具,为了达到所要求的尺寸精度及表面粗糙度,铸造成型后需要对模具进行切削加工。
陶瓷型精密铸造是在一般砂型铸造基础上发展起来的铸造新工艺。铸型型腔表面是一层特殊的陶瓷耐火材料,其表面细密光滑,生产出来的铸件精度可达IT8~ITl0级,表面粗糙度可达Ra1.25~10μm。在模具制造中,可用于制造塑料模、玻璃模、锻模以及拉深模等模具的型腔,也可用于浇铸锌合金模具。
压力铸造简称压铸,它是在高压下(比压约为5~150MPa)将液态或半液态合金快速地压入金属铸型中,并在压力下凝固以获得铸件的方法。压力铸造在金属熔液固化的全部过程一直承受着外界压力,因此,这种铸造就需要庞大的设备。压铸件的精度及表面质量较高,尺寸精度达IT11~IT13,表面粗糙度可达Ra1.6~6.3μm,通常不经机械加工即可使用,但压铸设备费用较高。压铸工艺主要用来制造对尺寸精度、表面质量要求较高的、尺寸较小的模具及型腔嵌件。
实型铸造又称汽化模铸造,(Full-Mould,简称FM法)是用聚苯乙烯泡沫塑料模样(包括浇注系统)代替木模(或金属模)进行砂型铸造,由于浇注时模样迅速汽化、燃烧而消失,使金属液充填了模样的位置、冷却凝固形成铸件。因为发泡聚苯乙烯比木材便宜,机械加工也比木模容易,所以,模型费用比木模费用便宜得多。这种方法铸件尺寸精度优于普通砂型铸造,特别适用于生产数量少,表面要切削加工的制件,如汽车覆盖件模具中的大型铸件最适合采用这种方法。
实践证明,在模具制造中,没有哪一种加工方法能适应所有的要求。在选用加工方法时,需要充分了解各种加工方法的特点,结合判断其加工的可能性和局限性,选取与要求相适应的方法进行加工。为了发挥各种加工方法的优点,在模具制造中应把其中一种加工方法和其他加工方法综合应用,以达到良好的加工效果。
4.模具制造过程
模具制造的过程:模具标准件、坯料准备→模具零件粗加工→热处理→模具零件精加工→模具装配。
一副模具的零件多达100个以上。如冲模由凸凹模、导向、顶出等部分组成;注射模及压铸模由型腔部分的定模以及型芯部分的动模,及导向、顶出、支撑等部分组成。其中除了标准件可以外购,直接进行装配外,其他零件都要进行加工。
坯料准备是为各模具零件提供相应的坯料,其加工内容按原材料的类型不同而异。对于锻件或切割钢板要进行6个面加工,除去表面黑皮,将外形尺寸加工到要求,磨削两平面及基准面,使坯料平行度和垂直度符合要求。直接应用标准模块,则坯料准备阶段不需要再进行任何加工,是缩短制模周期的最有效方法。模具设计人员应尽可能选用标准模块。在不得已的情况下,对标准模块进行部分改制加工。若基准面发生变动,则需重新加工出基准面。
模具零件粗加工的任务主要是对坯料进行内外形状的加工,去除模具精加工前大部分的加工余量,一般采用车、刨、铣、磨、镗、钳工等加工。例如,按冲裁凸模所需形状进行外形加工,按冲裁凹模所需形状加工型孔、紧固螺栓及销钉孔。又如按照注射模型芯的形状进行内、外形状加工,或按型腔的形状进行内形加工。
热处理是使经初步加工的模具零件半成品达到所需的硬度。模具零件的热处理方法有淬火、回火、正火、退火和表面热处理,它们的作用是改变材料力学性能。
模具零件的精加工是对淬硬的模具零件半成品进一步加工,以满足尺寸精度、形状精度和表面质量的要求。针对模具零件精加工阶段表面粗糙度要求高、材料较硬的特点,大多数采用磨削加工和电加工。
无论是冲模或注射模都有预先加工好的标准件供模具设计人员选用。现在,除了螺栓、销钉、导柱、导套等一般标准外,还有常用圆形和异形冲头、导销、推杆等各种标准件。此外,还开发了许多标准组合,使模具标准化达到更高的水平。模具制造中的标准化程度越高,则加工周期越短。
模具装配的任务是将已加工好的模具零件及标准件,按模具总装配图要求装配成一副完整的模具。在装配过程中,需对某些模具零件进行抛光和修整。试模后还需对某些部位进行调整和修正,使模具生产的制件符合图样要求,而且模具能正常地连续工作,模具加工过程才结束。在整个模具加工过程中还需对每一道加工工序的结果进行检验和确认,才能保证装配好的模具达到设计要求。
目前,各类模具从粗、精加工到装配技术和调试,都发展和配备了各种形式和规格的高效精密加工设备,基本上实现了机械化及自动化生产。加工装备除有光学控制、计算机程序控制的精密成型磨床、坐标镗床、坐标磨床、多轴成型铣床外,电火花加工工艺、数控线切割机床加工、电解加工等都有了迅速的发展,为模具制造提供了良好的装备。