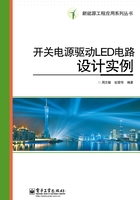
2.3 白光LED驱动方案比较
2.3.1 白光LED串联与并联驱动方案
因为白光LED可以采用串联或并联连接方式,两种解决方案各有优缺点。并联方式的缺点是LED电流及亮度不能自动匹配。串联方式保持固有的匹配特性,但需要更高的供电电压。红光和绿光LED的正向压降为1.8~2.4V(典型值),一些常用电池即可提供足够高的电压,直接驱动这些LED。然而,白光LED的正向压降为3~4V(典型值),通常需要一个独立电源供电。
在串联配置中,LED的数量受驱动器的最高电压限制,若最高电压为40V。在串联配置中根据白光LED的正向电压,这一最高电压最多能够驱动10~13只白光LED,驱动电流的范围是连续状态的10~350mA。这种配置的优点是:串联白光LED可以用单线传输电流。缺点是:当PCB空间受限时(特别是高功率时),铜导线上的电流密度是个问题,而且如果在串联模式中一只白光LED发生故障,所有白光LED都将被关掉。但是,从设计角度看,如果有n只白光LED,就要将电池电压提升到n×VF,所以必须采用升压结构,可以利用电感元件精确地监控电流斜率,从而限制了非受控瞬间电流产生的EMI。典型升压拓扑结构如图2-53所示。

图2-53 典型升压拓扑结构
在并联配置中,特定阵列中的白光LED数量受到驱动器封装水平和连接器引脚数量的限制。另外,在白光LED并联时,必须对每只白光LED进行电流控制,以确保各白光LED之间的匹配非常适合特定应用。实际上,2只白光LED电流不一致超出10%以上,将影响彩色LCD的显示图像的质量(白光LED作为LCD的背光源)。在串联配置的2只白光LED中并不存在2只白光LED电流不一致的问题,因为流过2只白光LED的电流是相同的。
此外,并联配置能够利用电荷泵技术,用2个陶瓷电容将能量从电池传输到白光LED阵列。除了电荷泵变换器以外,每只白光LED控制器还包含一个电流镜像,此电流镜像的性能是白光LED间良好匹配的关键。基于电荷泵的LED驱动器框图如图2-54所示,基于电池和专用电流源进行能量转换和调节的电荷泵,在进行电流源优化设计后可使白光LED电流不受正向电压和输入电源变化的影响。

图2-54 基于电荷泵的LED驱动器框图
另外,因为电荷泵是基于电压变换的,所以电流本身不是自动控制的,需要在芯片设计阶段特别慎重,以免在电路工作中出现大量EMI。EMI问题不仅限于电荷泵结构,如果芯片设计不良,或电感的质量不足以防止EMI时,电感式升压变换器更容易产生EMI问题。尤其由于成本原因,电感没有进行屏蔽,而且大量电磁场会因为线圈和磁泄漏而辐射到环境中。在设计初期使用恰当的屏蔽电感器比重新设计PCB布局和布线来解决EMI问题更有效。
同样地,采用最好的陶瓷电容比在项目接近完成时检查设计更加重要,虽然起初看起来设计的电路成本像是高一点。例如,低成本的电容(ESR=1Ω)会在输出200mA的LED驱动器电源端VBAT产生500mV的毛刺,这是PCB布局难以弥补的致命问题。
尽管设计一个能够在任何正向电流和配置情况下驱动白光LED的电路在技术上是可行的,但成本是十分昂贵的。开发一种处理特定需要、具有合理的额外特性或技术容限的驱动电路更经济有效,所以市场上出现了各种系列的LED驱动器。另外的一个趋势是采用微型封装技术减小应用于LED驱动器的芯片尺寸,新的芯片大小是2mm×2mm,仅0.55mm厚,能进一步减小占板面积。
目前的技术趋势是通过改进材料和封装来改进LED,减小相同工作电流下的正向压降,最终能够直接用单节带电流源的锂离子电池驱动LED,并控制LED电流。红色和琥珀色LED已实现上述目标,而一些白色LED的最大正向电压已接近3.2V。下一步将是设计出新的变换器,以使采用这种低VF的LED获得最高效率。
无论采用并联方式还是串联方式,大多数便携式电子设备的电池电压都不足以驱动LED,所以需要升压变换器。电荷泵利用电容实现电压转换,以提供高于电源电压或与电源电压反向的输出电压,电荷泵内部结构相对复杂,但外部元件可能较少,尺寸小、成本低。电荷泵是一个电压源,其数值取决于电容和开关数量。因此,在不大幅提高复杂度的情况下,达到较高输出电压更为困难。在这种情况下,要对LED进行并联而不是串联,要确保LED电流稳定,可通过附加电流源或限流电阻对LED电流进行匹配,确保LED之间的电流差异微乎其微。当精确度处于次要地位时,最好使用限流电阻来减少连接数量并降低复杂度。电荷泵的主要缺点在于其效率。开关和电容器的数量决定了电荷泵的增益。此增益通常为1.5倍压或2倍压。简单的方程给出了理想效率的计算方法如下:

图2-55 效率与电池电压的关系曲线
实际上,VOUT不可能等于N×VIN,因为确保内部电路正确偏置的最小压降在于驱动器本身,图2-55显示了电感升压变换器(此处为NCP5006)与有两倍压电荷泵之间的效率差别。
基于电荷泵的白光LED驱动器限制电源电压通常为5.5V或6V,这在一些应用中是极为重要的限制。因某些电感式升压变换器与电感器无须连接到同一个电源上,如NCP5006、NCP5007。电路电源电压为5.5V,但是功率开关最高电压为22V。由于电路的内部结构不同,因此在应用中可以采用低压稳压源为其供电,而电感器则需连接到更高的电池电压上。
基于电荷泵的白光LED驱动电路一个重要的参数是LED驱动器产生的噪声,因为电容器要进行充电、放电,所以电荷泵是大电流毛刺的来源。要减弱这种影响,必须设置高性能的输入滤波电路。基于电感式升压变换器的白光LED驱动器,由于存在电感,会引起电磁干扰。通常情况下,改变开关频率可减少干扰,但是频率值取决于变换器的工作条件。采用电感式升压变换器及电荷泵构成的典型LED驱动器的参数如表2-4所示。
表2-4 典型LED驱动器参数
2.3.2 白光LED驱动电路拓扑选择
白光LED驱动电路拓扑有升压变换器或电荷泵两种电路拓扑可供选择,选择的重点是考虑两种解决方案所有的具体因素。不同的最终应用对白光LED驱动器的要求可能差别极大,这点非常重要。若用白光LED作为LCD背光源,组件高度可能是最重要的设计参数,而对于个人数字助理(PDA)显示器,最重要的设计参数则可能是效率问题。采用TPS60230电荷泵驱动白光LED典型应用电路如图2-56所示。TPS60230由锂离子电池直接供电,典型输入电压范围为2.7~6.5V,可同时为最多5只白光LED供电,每只白光LED电流为20mA。

图2-56 TPS60230电荷泵驱动白光LED典型应用电路
采用TPS61062升压变换器驱动白光LED典型电路如图2-57所示。图2-57所示的升压变换器是IC技术的最新开发成果之一,作为全面集成的同步升压变换器,不用外接肖特基二极管就能够实现尺寸最小的解决方案,所需的外部组件数量最少。

图2-57 TPS61062升压转换器驱动白光LED典型电路
1.电荷泵与升压变换器效率比较

图2-58 电荷泵解决方案的典型效率曲线
基于图2-56与图2-57所示的解决方案,几乎很难说哪一种解决方案就是一个高效的解决方案,这是因为整体效率取决于白光LED正向电压、锂离子电池放电特性以及白光LED电流等具体应用参数等。对于基于电荷泵解决方案的典型效率曲线如图2-58所示。当变换器工作在1倍压模式下时,增益为1,输入电压范围从4.2V降至3.6V不等,效率水平高于75%,如图2-58所示。在1倍压模式下,电荷泵的作用就像LDO一样,输入电压经稳压降至白光LED正向电压,通常为3.1~3.5V。1倍压模式的另一优点是,开关器件不工作在开关状态,因此可以避免EMI问题。
但是,根据LED正向电压以及驱动器IC内部电压下降的情况不同,在驱动器从“1倍压模式”转为升压模式(boostmode)而采用的增益为1.5倍压时,效率会大幅下降。在升压模式下,开关器件工作在开关状态,输出电压为输入电压的1.5倍,这需要调节以降至白光LED所需正向电压的水平,这样也降低了效率。因此,驱动器工作在1倍压模式下的时间越长,电荷泵效率就越高。
与电荷泵解决方案不同,升压变换器TPS61062解决方案的典型效率曲线如图2-59所示。在锂离子电池的整个输入电压范围内效率均达到75%~80%。某些升压变换器解决方案在使用外部校正二极管的情况下其效率甚至高达85%,若TPS61062驱动白光LED少于5只,那么效率还会提高,因为输入到输出电压转换比较低。总体说来,升压变换器的效率比电荷泵解决方案略高,特别在为4只以上白光LED供电时更是如此。

图2-59 升压转换器TPS61062解决方案的典型效率曲线
2.电荷泵与升压变换器占板面积比较
过去,电荷泵解决方案有明显的优势,这主要是由于升压变换器采用较大的电感器和外部肖特基二极管。随着最新技术的发展以及集成度越来越高,升压变换器的解决方案尺寸大小也达到与电荷泵解决方案大致相当的水平。由于电荷泵驱动器所需的引脚数量较大,因此器件封装也相应较大,需要两个外部泵电容,在这种情况下,电荷泵解决方案的占板面积大小与升压变换器相当甚至还要再大些。如果将升压变换器的开关频率上升至高达1MHz,就能使用小型的电感器和小容量的输出和输入电容。例如,TPS61062器件可由内部控制回路控制电感器电流,在正常工作时小于最大交换电流。这就可采用较小的电感器,其最大额定电流刚好达到电感器的最大峰值电流。例如,驱动4只白光LED时,饱和电流为200mA的电感器就足够了。如果没有特定的内部环路设计,电感器饱和电流必须为400mA额定值,这就要求更大的电感器,而导致更大的占板面积。
3.电荷泵与升压变换器组件高度比较
当要求组件高度小于1mm的情况下,电感器的体积会相当大。因此当需要组件高度必须小于1mm时,电荷泵解决方案是更好的选择。
4.电荷泵与升压变换器EMI比较
在考虑EMI问题时,应分析升压变换器中电感器所带来的EMI问题。通常说来,可能的电磁辐射不会是大问题,因为RF(Radio Frequency,射频)敏感区周围的电感器是屏蔽的。电感式升压变换器造成EMI问题的原因有:输入和输出电压滤波不足而产生的传导干扰;印制电路板(PCB)布局或布线不合理而产生的电磁干扰。
在锂离子电池供电的无线电子设备中,白光LED驱动器的开关噪声进入RF系统,与白光LED驱动器的输入耦合。带有脉动输入电流的白光LED驱动器,其输入端直接连接至电池电极端,由于RF部分也由电池供电,因此白光LED驱动器输入端的开关噪声也存在于电池连接处,同时也存在于RF电路的输入端,这会导致严重的干扰。
为了明确哪种白光LED驱动器解决方案在传导EMI方面的性能更好,应比较升压变换器与电荷泵解决方案的输入电压纹波。一种评估解决方案的办法就是用频谱分析仪检查输入端,如果器件以固定的开关频率工作,那么频谱将显示基波的开关频率及其谐波。如图2-60所示,显示了用频谱分析仪测量升压变换器TPS61062(带有标准的1μF输入电容)输入端的频谱。由图2-60可知谐波在更高的开关频率上。为了将RF部分的干扰降至最低,基波频率及其谐波应尽可能高,振幅则应保持较低。这是因为变换器的开关频率会与发射机的载频相混合,使边带也有载频。边带出现在发射机的输出频带中,刚好比发射机频率高或低一个开关频率。开关频率越低,边带离载频就越近,可降低发射机的信噪比。开关频率越高,边带离载频就越远,并加大发射机的信噪比。当然,变换器开关频率基波的振幅越低,信噪比就越高。正因为如此,固定的变换器开关频率大于或等于1MHz时,通常适合大多数应用的要求。

图2-60 开关频率为1MHz的升压变换器的输入频谱
在相同设置下,电荷泵解决方案的输入纹波电压是升压变换器解决方案的两倍。这是由于电荷泵工作于1.5倍压模式下会产生几乎为方形波的输入电流。作为输入滤波器,电荷泵只有输入电容,而升压变换器带有电感及输入电容,可更好地完成输入滤波器的工作,从而实现较低的输入电压纹波。为了进一步降低输入电压纹波,在采用升压变换器以及电荷泵解决方案时最有效的方法就是增加输入电容的值。对于非常敏感的应用,还可考虑增加额外的LC输入滤波器或采用较小的铁氧体磁珠。
可以清楚地看到,电荷泵解决方案满足不了所有的应用,升压变换器解决方案也是如此。选择解决方案时要根据具体的最终应用要求和关键参数来考虑。此外,电荷泵解决方案在EMI方面并不优于电感式升压变换器解决方案。如表2-5所示,归纳了选择电荷泵或电感式升压变换器解决方案时的重要选择标准。
表2-5 电荷泵或电感式升压变换器解决方案比较