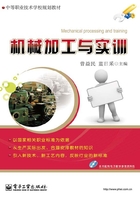
1.2 车刀切削部分的几何参数
一、车刀的组成
(一)车刀的主要部分
外圆车刀是最基本、最典型的刀具。如图1-3所示,它由刀体8和刀柄7组成。刀体用来切削,又称切削部分;刀柄用来将车刀夹固在车床刀架上。车刀切削部分一般由三个表面、两个切削刃和一个刀尖组成。

1—副后面;2—副切削刃;3—前面;4—主切削刃;5—刀尖;6—后面;7—刀柄8—刀体;9—圆柱销;10—刀片;11—楔块;12—夹紧螺钉
图1-3外圆车刀
1.三个表面
(1)前面Aγ 刀具上切屑流过的表面称为前面,也称为前刀面。
(2)后面Aa 与工件上的过渡表面相对的表面称后面,也称主后面。
(3) 副后面3) A′a 与工件上的已加工表面相对的表面称副后面 。
2.两个切削刃
(1)主切削刃S 前面与后面的交线为主切削刃。它承担着主要的切削工作。
(2)副切削刃S′ 前面与副后面的交线为副切线削刃。通常,靠近刀尖处的副切削刃起微量切削作用,在大进给量切时,副切削刃也起主要的切削作用。
3.刀尖
刀尖是主、副切削刃的交点。通常,刀尖用短直线或圆弧取代它,以提高刀具的使用寿命。
不同类型的刀具,其刀面、切削刃的数量不完全相同。例如,车床上常用的切断刀就有两个副切削刃。
(二)常用车刀的结构
图1-3所示为车刀常用结构。图1-3(a)是硬质合金刀片焊接式车刀;图1-3(b)为高速钢整体式车刀,刀体切削部分靠刃磨成形;图1-3(c)是将具有若干个切削刃的硬质合金刀片紧固在刀体上,称机械夹固(简称“机夹”)式车刀。
金属切削刀具的种类很多,形状和结构较复杂,且各不相同。但对各种复杂刀具或多齿刀具,其主要切削部分的几何形状都相当于一把车刀的切削部分。如图1-4所示,钻头可看作两把一正一反对称装夹后,同时车削孔壁两侧的车刀;图1-5所示的铣刀虽然形状复杂,实际上是由多把车刀组合而成,一个刀齿可看作一把车刀。因此,本书将车刀作为研究的主要对象。

1—主切削刃;2—副切削刃
图1-4 钻头与车孔刀的对比

1—主切削刀;2—副后面;3—副切削刀;4—前面
图1-5铣刀和车刀对比
二、确定车刀几何角度的辅助平面
为了便于设计时在图样上标注和制造以及刃磨时测量刀具的几何角度,需要假定三个辅助平面作为基准,即基面、切削平面和正交平面,它们共同构成刀具静止参考系,如图1-6所示。

图1-6 刀具静止参考系
(1)基面pr 基面pr是通过主切削刃上的选定点而又垂直于该点切削速度(不考虑进给运动时的切削速度)的平面。基面平行于车刀底面,底面是制造、刃磨、测量和装夹车刀的基准面。
(2)切削平面ps 切削平面ps是通过主切削刃上的选定点与主切削刃S相切并垂直于基面pr的平面。切削平面是包含相对运动速度的平面,若不考虑进给运动的影响,相对运动速度的方向就是切削速度的方向。
(3)正交平面po 正交平面po(也称主剖面)是通过主切削刃上的选定点并同时垂直于基面pr和切削平面ps的平面。
三、车刀的几何角度
刀具几何角度有标注角度(或称刃磨角度)和工作角度(或称实际切削角度)。
(一)刀具的标注角度
在刀具图样上标注的角度称为标注角度,也就是刀具制造和刃磨时控制的几何角度。刀具标注角度是在上述刀具静止参考系内度量的,如图1-7所示。
1.在正交平面po内测量的角度
(1)前角γo 前面与基面之间的夹角。
(2)后角αo 分主后角αo和副后角αo′,主后角αo是主刀后面与切削平面之间的夹角,副后角αo′是副刀后面与副切削平面之间的夹角。
(3)楔角βo 前面与主后面之间的夹角。
2.在基面pr内测量的角度
(1)主偏角Κr 主切削刃S与进给速度vf之间的夹角。
(2)副偏角Κr′ 副切削刃S′与进给速度vf反方向之间的夹角。
(3)刀尖角εγ 主切削刃S与副切削刃S′之间的夹角。其公式为

3.在切削平面ps内测量的角度
刃倾角λs主切削刃S与基面pr之间的夹角。前角和刃倾角均可为正值、负值或零。在正交平面po中,前面与基面重合时前角为零,车刀刀尖处于主切削刃上最高点时,刃倾角为正;刀尖处于主切削刃上最低点时,刃倾角为负值(图1-7)。图1-8所示为车刀刃倾角的三种不同情况。

图1-7 车刀的标注角度

图1-8 车刀的刃倾角
车刀有六个基本角度:前角γo、主后面αo、副后面αo′主偏角Κr、副偏角Κr′、刃倾角λs,两个派生角度:楔角βo和刀尖角εγ。
(二)刀具的工作角度
刀具的工作角度是考虑实际装夹条件和进给运动的影响而确定的角度。当考虑实际装夹和进给运动的影响时,刀具标注角度的静止参考系将发生变化而称为刀具工作参考系。因此,刀具工作时的角度也随之变化而称为工作角度。
(1)装夹对刀具工作角度的影响 如图1-9(a)所示,刀尖对准工件中心安装时,设切削平面(包含切削速度νc的平面)与车刀底面相垂直,则基面与车刀底面平行,刀具切削角度无变化;图1-9(b)为刀尖装夹得高于工件中心时,切削速度νc所在平面(即切削平面)倾斜一个角度τ,则基面也随之倾斜一个角度τ,从而使前角γo增大了一个角度τ;后角αo减小了一个角度τ。反之,当刀尖装夹得低于工件中心时,则前角γo减小,后角αo增大,如图1-9(c)所示。
(2)进给运动对工作角度的影响 如图1-10所示,切削时若考虑进给运动,包含合成切削速度νe切削平面(称工作切削平面)倾斜一个角度,而垂直于工作切削平面的基面(称工作基面)则随之倾斜,从而导致刀具工作角度变化。实际车削的外圆表面是一个螺旋面,通过切削刃选定点的工作基面和工作切削平面都要倾斜一个螺旋升角ψ,使前角γo增大一个角度ψ,则后角αo减小一个角度ψ。一般车削时,由于进给量比工件直径小得多,ψ值很小,所以对车刀工作前、后角的影响可忽略不计。但车削导程较大的螺纹时,如梯形螺纹,矩形螺纹和多线螺纹,则必须考虑螺纹升角ψ对加工的影响。
四、车刀的刃磨与几何角度的测量
(一)车刀几何角度的刃磨方法
1.砂轮的选用
(1)磨料的选择 磨料选择的主要依据是刀具的材料和热处理方法。除手动工具外,大部分刀具材料用高速钢淬火后硬度在65HRC左右。刃磨硬质合金刀具通常选用绿色碳化硅磨料GC(旧TL),刃磨淬火高速钢刀具选用白刚玉WA(旧GB)或铬刚玉PA(旧GG)磨料。对于要求较高的硬质合金刀具(如铰刀等),可用人造金刚石D(旧JR)磨料。对于高钒高速钢工具,选用单晶刚玉 SA(旧 GD)磨料。
(2)砂轮粒度的选择 砂轮粒度选择的主要依据是刀具的精度和表面粗糙度要求,此外还要考虑磨削效率。一般刀具的表面粗糙度值 Ra 为0.4 ~0.1μm时,若分粗、精磨,则从磨削效率考虑,粗磨时应选粒度为46# ~60#的砂轮,精磨时应选粒度为80#~120#的砂轮。

图1-9 车刀刀尖装夹高度对工作角度的影响

图1-10 进给运动对工作前、后角的影响
(3)砂轮硬度选择 刃磨刀具时,砂轮硬度应选得软些。一般刃磨硬质合金刀具,硬度选用H(旧R2)、J(旧R3);刃磨高速钢刀具,硬度选用H(旧R2)、K(旧XR1)。
2.车刀几何角度的刃磨方法
(1)刃磨方法 如图1-11所示,刀尖角εγ为80°的外圆车刀,采用手工刃磨的方法。简述如下:
1)人站立在砂轮侧面,以防砂轮碎裂时,其碎片飞出伤人。
2)两手握刀的距离拉开,两肘夹紧腰部,可减小磨刀时手的抖动。
3)磨刀时,车刀应放在砂轮的水平中心,刀尖略微上翘约3°~8°,车刀接触砂轮后应作左右方向的水平移动。当车刀离开砂轮时,刀尖应向上抬起,以防磨好的刀刃被砂轮碰伤。
4)磨主后面时,刀柄尾部向左偏一个主偏角的角度,如图1-11(a)所示;磨副后面时,刀柄尾部向右偏过一个副偏角的角度,如图1-11(b)所示。

图1-11 车刀的刃磨
5)修磨刀尖圆弧时,通常以左手握车刀前端为支点,用右手转动车刀尾部,如图1-11(d)所示。
6)刃磨步骤:粗磨主后面和副后面,粗、精磨前面,精磨主后面和副后面,磨刀尖圆弧,角度测量,用油石手工研磨负倒棱及刀尖圆弧。
(2)注意事项
1)车刀刃磨时,不能用力过大,以防打滑伤手。
2)车刀的高低必须控制在砂轮水平中心,使刀具头部略向上翘,否则会出现负后角或后角过大等弊端。
3)车刀刃磨时应作水平的左右移动,以免砂轮表面出现凹坑。
4)在平形砂轮上磨刀时,应避免在砂轮侧面上磨。
5)砂轮磨削表面必须经常修整,使砂轮没有明显的跳动。对平形砂轮一般可用砂轮刀在砂轮上来回修整,如图1-12所示。

图1-12 用砂轮刀修整砂轮
6)磨刀时要求戴防护镜。
7)刃磨硬质合金车刀时,不可把刀体部分放入水中冷却,以防刀片突然冷却而碎裂。刃磨高速钢车刀时,应随时用水冷却,以防车刀过热退火而降低硬度。
8)在磨刀前,要对砂轮机的防护设施进行检查,如防护罩是否齐全,是否有托架的砂轮,其托架与砂轮之间的间隙是否恰当等。
9)重新安装砂轮后,要进行检查,经试转后才能使用。
10)刃磨结束后,应随手关闭砂轮机电源。
(二)车刀几何角度的测量
车刀标注角度可用角度样板、万能角度尺及量角台等进行测量。本书主要介绍量角台的使用方法。
1.车刀量角台的结构
车刀量角台是测量车刀标注角度的专用量角仪器,其形式很多,常用的量角台如图1-13所示。在支脚1上的圆形底盘2的周边,刻有从0起向左、右各100°的刻度,工作台5绕小轴7转动,转动角度由固定于工作台上的指针6读出。定位块4和导条3固定在一起,可在工作台的滑槽内平行移动。

1—支脚;2—圆形底盘;3—导条;4—定位块;5—工作台;6—指针;7—小轴;8—螺钉轴;9—大指针;10—销轴;11—螺钉;12—大刻度盘13—滑体;14—小指针;15—小刻度盘;16—小螺钉;17—旋钮;18—弯板;19—螺母;20—立柱
图1-13车刀量角台
立柱20固定在底盘上,其上有矩形螺纹。旋转螺母19,可使滑体13沿立柱的键槽上、下移动。小刻度盘15由小螺钉16固定在滑体上,用旋钮17可将弯板18锁紧在滑体上。松开旋钮,弯板以旋钮为轴,可向顺时、逆时针两个方向转动,转动的角度由固定于弯板18上的小指针14在小刻度盘15上示出。大刻度盘12转动角度由螺刻度盘上的大指针9在大刻度盘上示出,绕螺钉轴向顺、逆时针两面个方向转动,转动的极限位置由销轴10限制。当指针6、大指针9、小指针14都处于0°时,大指针的前面a和侧面b分别垂直于工作台的平面,而底面c平行于工作台的平面。
2.用车刀量角台测量车刀标注角度
(1)校准车刀量角台测量的原始位置 测量前应将量角台的大、小指针全部全部调整到零位,然后按图1-14把车刀平放在工作台上。此状态下车刀量角台位置为测量车刀角度的原始位置。

图1-14 测量车刀角度的原始位置
(2)主偏角的测量 从原始位置起,按顺时针方向转动工作台(工作台平面相当于基面pr),让主切削刃和大指针前面α紧密结合,如图1-15所示。此时,工作台指针在底盘上所指示的刻度值,即是主偏角的数值。

图1-15 测量车刀主偏角
(3)刃倾角的测量 测完主偏角后,使大指针底面c和主切削刃紧密贴合(大指针前面α相当于切削平面ps),如图1-16所示。此时,大指针在大刻度盘上所指示的刻度值,就是刃倾角数值。大指针在零位左边为+λs,在右边为-λs。

图1-16 测量车刀的刃倾角
(4)副偏角的测量 参照测量主偏角的方法,按逆时针方向转动工作台,使副切削刃和大指针前面α紧密贴合,如图1-17所示。此时,工作台指针在底盘上所指示的刻度值,就是副偏角的数值。

图1-17 测量车刀副偏角
(5)前角的测量 从图1-15测完车刀主偏角的位置起,按逆时针方向使工作台转90°,这时主切削刃在基面上的投影恰好垂直于大指针前面α(相当于正交平面po),然后让大指针底面c落在通过主切削刃上选定点A的前面上(紧密贴合),如图1-18(a)所示。此时,大指针在大刻度盘上所指示的刻度值,就是正交平面内前角的数值。指针在零位右边时为+γo,在左边时为-γo。
(6)后角的测量 测完前角后,向右平行移动车刀(这时定位块可能要移到车刀的左边,但仍要保证车刀侧面与定位块侧面靠紧),使大指针侧面b和通过主切削刃上选定点Aa的后面紧密贴合,如图1-18(b)所示。此时,大指针在大刻度盘上所指示的刻度值,就是正交平面内后角的数值。指针在零位左边为+αo,在右边为-αo。

图1-18 测量车刀的前角与后角