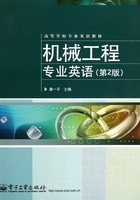
6.6 Ultrasonic Machining (USM)
Ultrasonic machining offers a solution to the expanding need for machining brittle materials such as single crystals, glasses and polycrystalline ceramics, and for increasing complex operations to provide intricate shapes and workpiece profiles. This machining process is non-thermal, non-chemical, creates no change in the microstructure, chemical or physical properties of the workpiece and offers virtually stress-free machined surfaces. It is therefore used extensively in machining hard and brittle materials that are difficult to cut by other traditional methods. The actual cutting is performed either by abrasive particles suspended in a fluid, or by a rotating diamond-plated tool. These variants are known respectively as stationary (conventional) ultrasonic machining and rotary ultrasonic machining (RUM).
Conventional ultrasonic machining (USM) accomplishes the removal of material by the abrading action of a grit-loaded slurry, circulating between the workpiece and a tool that is vibrated with small amplitude. The form tool itself does not abrade the workpiece; the vibrating tool excites the abrasive grains in the flushing fluid, causing them to gently and uniformly wear away the material, leaving a precise reverse form of the tool shape. The uniformity of the sonotrode-tool vibration limits the process to forming small shapes typically under 100 mm in diameter.
The USM system includes the Sonotrode-tool assembly, the generator, the grit system and the operator controls. The sonotrode is a piece of metal or tool that is exposed to ultrasonic vibration, and then gives this vibratory energy in an element to excite the abrasive grains in the slurry.[9] A schematic representation of the USM set-up is shown in Fig.6.5. The sonotrode-tool assembly consists of a transducer, a booster and a sonotrode. The transducer converts the electrical pulses into vertical stroke. This vertical stroke is transferred to the booster, which may amplify or suppress the stroke amount. The modified stroke is then relayed to the sonotrode-tool assembly. The amplitude along the face of the tool typically falls in a 20 to 50 μm range. The vibration amplitude is usually equal to the diameter of the abrasive grit used.

Fig.6.5 Schematic representation of USM apparatus
The grit system supplies a slurry of water and abrasive grit, usually silicon or boron carbide, to the cutting area. In addition to providing abrasive particles to the cut, the slurry also cools the sonotrode and removes particles and debris from the cutting area.