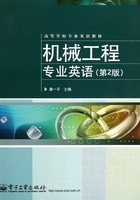
6.4 Electrochemical Machining (ECM)
Electrochemical metal removal is one of the more useful nontraditional machining processes. Although the application of electrolytic machining as a metal-working tool is relatively new, the basic principles are based on Faraday laws. Thus, electrochemical machining can be used to remove electrically conductive workpiece material through anodic dissolution. No mechanical or thermal energy is involved. This process is generally used to machine complex cavities and shapes in high-strength materials, particularly in the aerospace industry for the mass production of turbine blades, jet-engine parts, and nozzles, as well as in the automotive (engines castings and gears) and medical industries.[4] More recent applications of ECM include micromachining for the electronics industry.
Electrochemical machining (ECM), shown in Fig.6.3, is a metal-removal process based on the principle of reverse electroplating. In this process, particles travel from the anodic material (workpiece) toward the cathodic material (machining tool). Metal removal is effected by a suitably shaped tool electrode, and the parts thus produced have the specified shape, dimensions, and surface finish. ECM forming is carried out so that the shape of the tool electrode is transferred onto, or duplicated in, the workpiece. The cavity produced is the female mating image of the tool shape. For high accuracy in shape duplication and high rates of metal removal, the process is operated at very high current densities of the order 10–100 A/cm2, at relative low voltage usually from 8 to 30 V, while maintaining a very narrow machining gap (of the order of 0.1 mm) by feeding the tool electrode with a feed rate from 0.1 to 20 mm/min. Dissolved material, gas, and heat are removed from the narrow machining gap by the flow of electrolyte pumped through the gap at a high velocity (5 – 50 m/s), so the current of electrolyte fluid carries away the deplated material before it has a chance to reach the machining tool.

Fig.6.3 Schematic diagram of electrochemical machining process
Being a non-mechanical metal removal process, ECM is capable of machining any electrically conductive material with high stock removal rates regardless of their mechanical properties.[5] In particular, removal rate in ECM is independent of the hardness, toughness and other properties of the material being machined. The use of ECM is most warranted in the manufacturing of complex-shaped parts from materials that lend themselves poorly to machining by other, above all mechanical methods. There is no need to use a tool made of a harder material than the workpiece, and there is practically no tool wear. Since there is no contact between the tool and the work, ECM is the machining method of choice in the case of thin-walled, easily deformable components and also brittle materials likely to develop cracks in the surface layer.