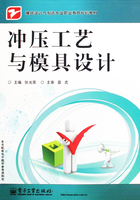
第二节 冲裁间隙
在冲裁过程中,材料受到弯曲的作用,工件产生穹弯而不平整。由于冲裁变形的特点,在冲裁端面具有明显的4个特征区(图1-3),即a(塌角)、b(光亮带)、c(断裂带)和d(毛刺)。

图1-7 冲裁间隙示意图
冲裁件的4个特征区在整个端面上所占比例的大小并非一成不变,而是随着材料的力学性能、冲裁间隙、刃口状态等条件不同而变化的。
冲裁间隙的大小对冲裁质量、模具寿命、冲裁的影响很大,它是冲裁工艺与模具设计的一个重要工艺参数。
冲裁间隙系指冲裁的凸模与凹模之间的间隙,单面间隙用c表示,双面间隙用z表示(图1-7)。
一、间隙的影响
1.对冲裁质量的影响
冲裁件的质量主要是指断面质量、尺寸精度和弯曲度。
(1)对断面质量的影响
冲裁断面应平直、光圆角小;光亮带应占有一定的比例,毛刺较小,冲裁件表面应尽可能平整,尺寸应在图样规定的公差范围之内。影响冲裁件质量的因素有:凸、凹模具间隙值及其分布的均匀性,以及精度、材料性能等,其中,间隙值与分布的均匀程度是主要因素。
冲裁时,间隙适合,可使上下裂纹与最大切应力方向重合,此时产生的冲裁断面比较平直、光洁、毛刺比较小,制件的断面质量比较好(图1-8)。间隙过大或过小将导致上、下裂纹中间不重合。间隙过小时,上下裂纹中间部分被第二次剪切,在断面上产生撕裂面,断面2撕裂,使光亮带在断面出现挤长毛刺。间隙过大,料板所受弯曲与拉申均变大,断面容易撕裂,使光亮带所占比例减小,产生较大塌角,粗糙度断裂带斜度增大,毛刺大而厚,难以除去,使冲裁断面质量下降。

1—断裂带;2—光亮带;3—圆角带
图1-8 间隙对工件断面质量的影响
(2)对尺寸精度的影响
冲裁的尺寸精度是指冲裁件实际尺寸的差值,差值越小,精度越高。该差值包括两个方面的偏差,一方面是冲裁件相对凸模或凹模尺寸的偏差,另一方面是模具本身的制造偏差。
冲裁件相对于凸模或凹模尺寸的偏差,主要是由于冲裁过程中,材料受到拉深、挤压、弯曲等作用而引起的变形,在工件脱落后产生的弹性恢复造成的。偏差值可能是正的,也可能是负的。影响这一偏差值的因素主要是凸、凹模间隙。
当间隙较大时,材料受拉深作用增大,冲裁完毕后,因材料的弹性恢复,冲件尺寸向实体方向收缩,使落料件尺寸小于凹模尺寸,而冲孔件的孔径大于凸模尺寸;当间隙较小时,材料的弹性恢复使落料件尺寸增大,而冲孔件的孔径变小。冲裁件的尺寸变化量的大小还与材料性能、厚度、轧制方向、冲件形状等因素有关。模具制造精度及模具刃口状态也会影响冲裁件质量。
(3)对弯曲度的影响
冲裁过程中由于材料受到弯矩作用产生弯曲,若变形达到塑性弯曲,冲裁件脱模后即使回弹,工件仍残留有一定弯曲度。这种弯曲程度跟凸、凹模间隙的大小、材料性能及材料支撑方法有关。图1-9为1.6mm厚度钢板上冲制φ20mm的冲件的实验所求得的凸、凹模刃口双面间隙与冲件曲率半径的关系。

图1-9 间隙与冲件曲率半径
2.对模具寿命的影响
冲裁模具的寿命是以冲出合格制品的冲裁次数来衡量的,可分为两次刃磨间的寿命和全磨损后总的寿命。
在冲裁过程中,模具刃口处所受的压力非常大,使模具刃口和板材的接触面之间出现局部附着现象,产生附着磨损,其磨损量与接触压力、相对滑动距离成正比,与材料屈服强度成反比,被认为是模具磨损的主要形成原因。
当间隙减小时,接触压力(垂直力、侧压力和摩擦力)会增大,摩擦距离增长,摩擦发热严重,导致模具磨损加剧(图1-10),使模具与材料之间产生粘结现象,会引起刃口的压缩疲劳破坏,使之崩刃。间隙过大时,板材弯曲拉深相对增加,使模具刃口端面上的正压力增大,容易产生崩刃或塑型变形,使磨损加剧。可见,减小材料间摩擦,并减缓间隙不均匀的不利因素,可以提高模具寿命。

图1-10 间隙与磨损的关系
从图1-10可看出,凹模端面磨损比凸模大,这是因为凹模端面上材料的滑动比较自由,而凸模下面的材料沿板面方向滑动受到限制的原因。而凸模侧面的磨损最大,是因为凸模侧面受到的卸料作用的长距离摩擦,加剧了侧壁的磨损。若采用较大间隙,可使孔径在冲裁后的回弹增大,减小卸料时与凹模侧面的摩擦,从而减小凸模侧面的磨损。
模具刃口磨损,导致刃口的钝化和间隙增加,使制件尺寸精度降低,冲裁能量增大,断面粗糙,毛刺增大。为了提高模具寿命,一般需采用较大间隙,若制件要求精度不高时,采用合理大间隙,模具寿命可以提高。若采用小间隙,就必须提高模具硬度与制造精度,对冲模刃口进行充分润滑,以减少磨损。
3.对冲裁力的影响
一般认为,增大间隙可以降低冲裁力,而减小间隙会使冲裁力增大。当间隙合理时,上下裂纹重合,最大剪切力较小。而小间隙时,材料所受力矩和拉应力减小,压应力增大,材料不易产生撕裂,上下裂纹不重合产生二次剪切,使冲裁力、冲裁功有所增大;增大间隙时材料所受力矩与拉应力增大,材料易于剪裂分离,故最大冲裁力减小,如对冲裁件质量要求不高,为降低冲裁力、减少模具磨损,倾向于取偏大的冲裁间隙。
二、间隙的确定
由以上分析可见,冲裁间隙对冲裁件质量、冲裁力、模具寿命等都有很大的影响,设计模具时应选用合理间隙值。但分别符合这些要求的合理间隙值并不相同,只是彼此接近。生产中通常是选择一个适当的范围作为合理间隙。这个范围的最小值称为最小合理间隙,最大值称为最大合理间隙。考虑到生产过程中的磨损使间隙变大,故设计与制造模具时,通常采用最小合理间隙值。确定合理间隙值有如下两种方法。

图1-11 合理冲裁间隙的确定
1.理论确定法
理论确定法的主要依据是保证裂纹重合,以获得良好的冲裁断面。图1-11是冲裁过程中开始产生裂纹的瞬时状态。由图中几何关系可得出计算合理间隙的公式:
z=20(t-h0)tanβ=2t(1-h0/t)tanβ
式中,
t——板材厚度(mm);
h0/t——产生裂纹时凸模相对压入的深度(mm);
β——裂纹与垂线间的夹角。
由上述可知,间隙z与板材厚度、相对压入深度h0/t、裂纹方向角β有关。而h0、β又与材料性质有关,表1-1为常用材料的h0/t与β的近似值。由表可知,影响间隙值的主要因素是板材力学性能及其厚度。板材越厚、越硬或塑性越差,h0/t值越小,合理间隙值越大;材料越软,h0/t值越大,合理间隙值越小。
表1-1 h0/t与β值(单位:mm)

因为计算法在生产中使用不方便,故目前普遍使用查表选取法。
2.查表选取法
综上所述,间隙的选取主要与材料的种类、厚度有关,由于多种冲压件对其断面质量和尺寸精度的要求不同,以及生产条件的差异,在实际生产中很难有一种统一的间隙数值,而应区别情况、分别对待,在保证冲裁件断面质量和尺寸精度的前提下,使模具寿命最高。国内工厂常用的间隙值见表1-2、表1-3和表1-4。表1-2~表1-4给出了汽车、拖拉机、电器仪表和机电行业推荐的几种间隙值。
表1-2 冲裁模初始双面间隙z(z=2c)(单位:mm)

注:1.冲裁皮革、石棉和纸板时,间隙取08钢的25%。
2.c为单位间隙。
表1-3 冲裁模初始双面间隙z(z=2c)(单位:mm)

注:1.初始间隙的最小值相当于间隙的公称数值。
2.初始间隙的最大值是考虑到凸模和凹模的制造公差所增加的数值。
3.在使用过程中,由于模具工作部分的磨损,间隙将有所增加,因而间隙使用的最大值要超过表列数值。
4.c为单面间隙。
表1-4 冲裁模刃口双面间隙z(z=2c)(单位:mm)

表1-5是原机械工业部的《冲裁间隙》指导性技术文件(JB/Z271—1986)推荐的间隙值。该文件将间隙分成三类。其中,Ⅰ类适用于对断面质量与冲裁件精度均要求高的工件,但模具寿命较低;Ⅱ类适用于端面质量、冲裁件精度要求一般,以及需继续塑性变形的工件;Ⅲ类适用于断面质量、冲裁件精度均要求不高的工件,但模具寿命较长。
表1-5 冲裁单面间隙比值c/t(单位:%)

注:1.本表试用于厚度为10mm以下的金属材料。考虑到料厚对间隙比值的影响,将料厚分成0.1~1.0mm、1.2~3.0mm、3.5~6.0mm、7.0~10.0mm四档,当料厚为0.1~1.0mm时,各类间隙比值取下限值。并以此为基数,随着厚度的增加,而逐档递增(0.5~1.0)%t(有色金属和低碳钢取小值,中碳钢和高碳钢取大值)。
2.凸、凹模的制造偏差和磨损均使间隙变大,故新模具应取最小间隙值。
3.其他金属材料的间隙比值可参照表中抗剪强度相近的材料选取。
4.非金属材料:红纸板、胶纸板、胶布板的间隙比值分两类,相当于表中Ⅰ类时,取(0.5~2)%t;相当于Ⅱ类时,取(>2~4)%t;纸、皮革、云母纸的间隙比值取(0.25~0.75)%t。